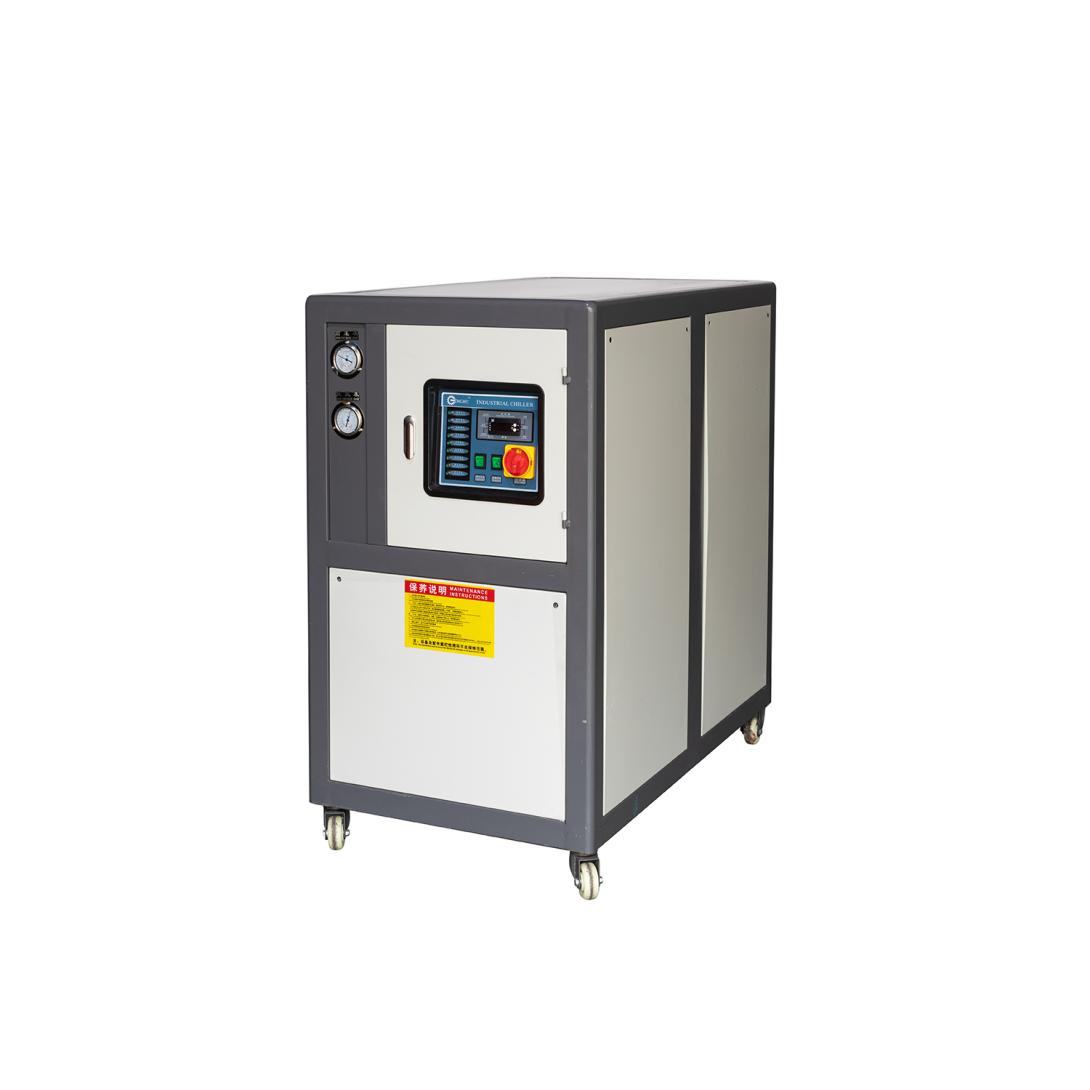
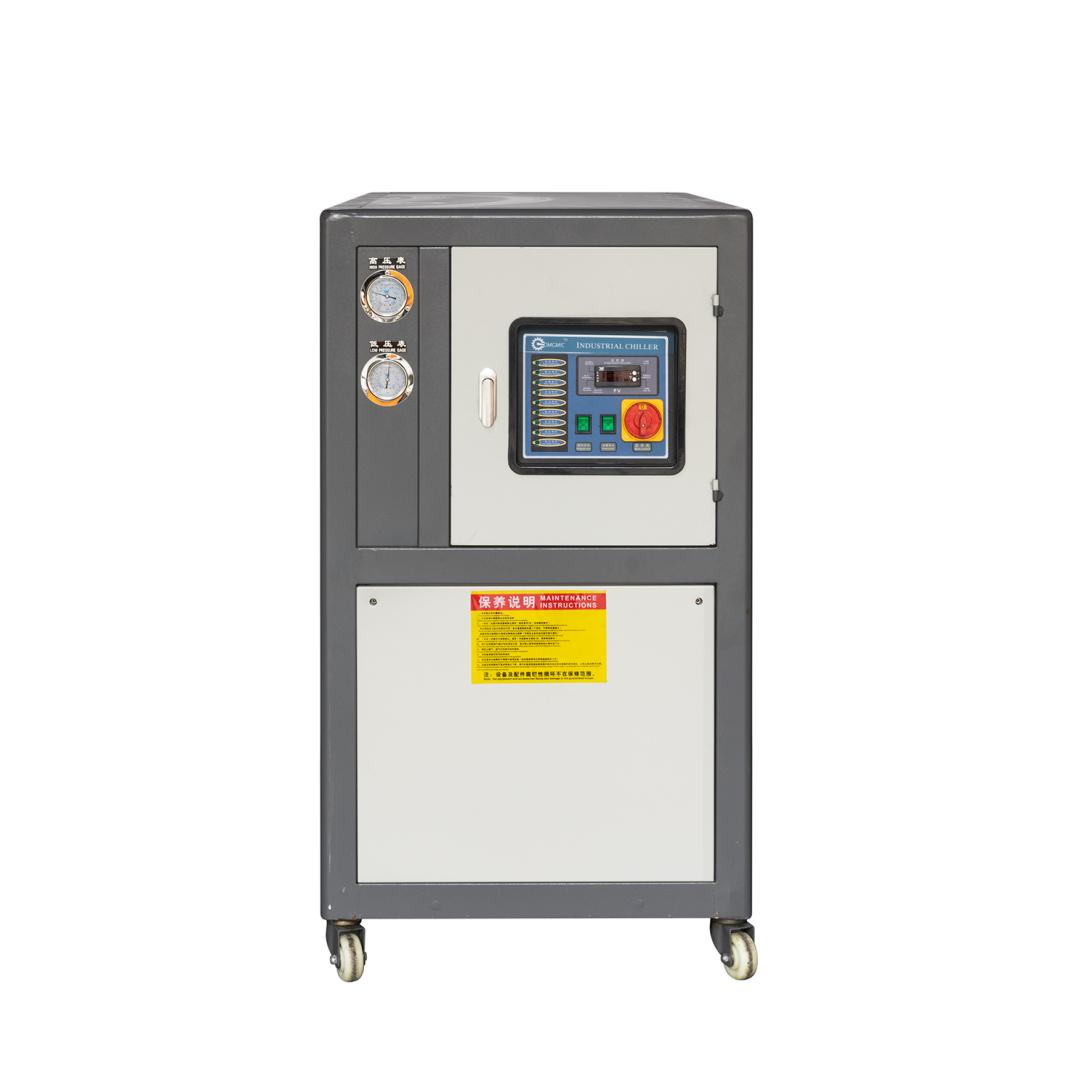
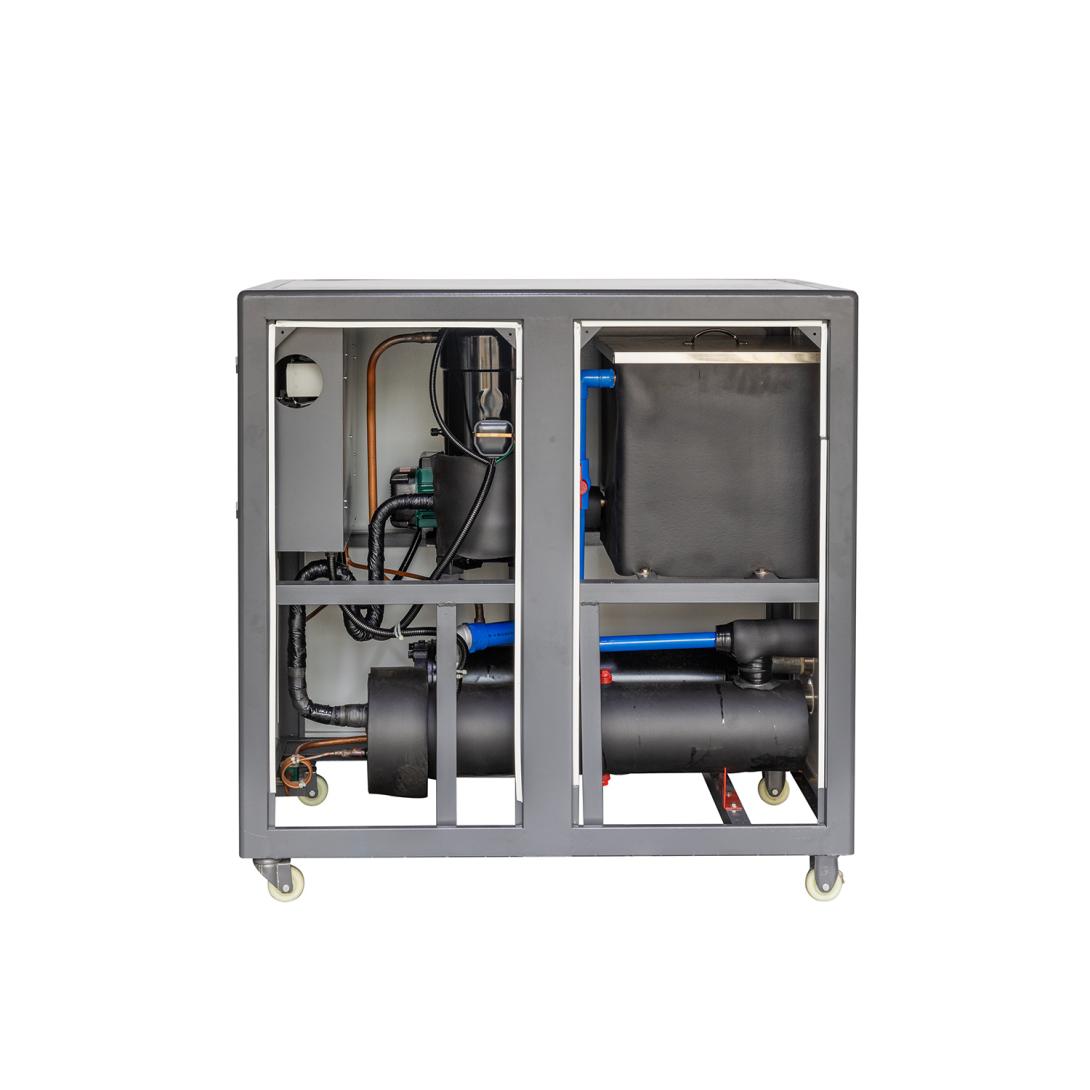
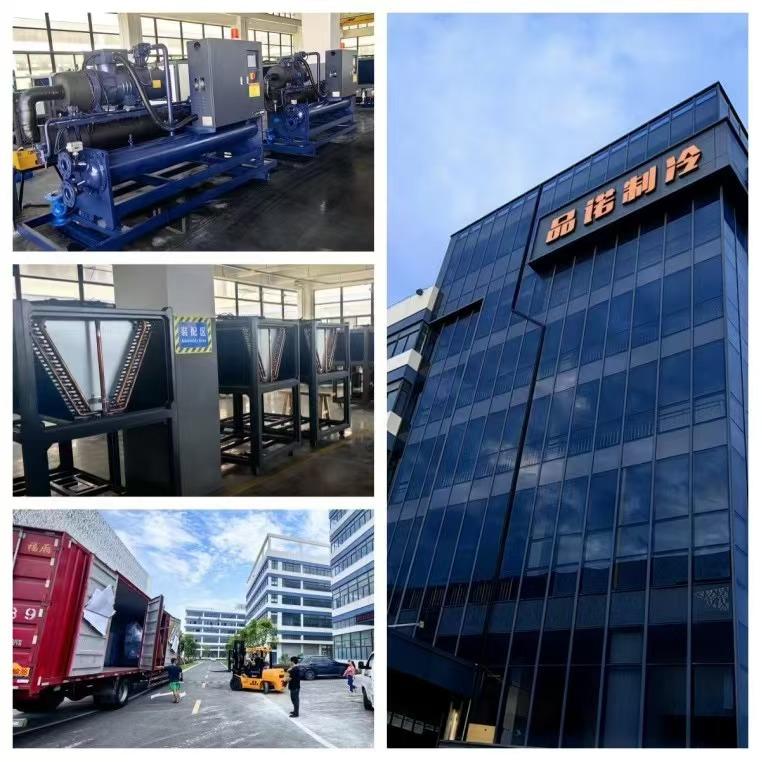
Applied in the plastic industry:
Plastic molding, injection molding, extrusion molding, bottle blowing, thermoforming, mechanical industry: laser technology, welding, mechanical cutting processing, non cutting processing, casting, electroplating, electronics industry: surface treatment, electroplating, electrophoresis, medical equipment, electronics industry, circuit board production, electronic chip manufacturing, chemical industry and other industries: chemical, papermaking, pharmaceutical, food processing, aluminum profiles, aluminum alloys, tempered glass, coated glass production, ultrasonic cleaning, jewelry processing, leather and fur processing, ink production, aquaculture.
Main features:
Low noise, high temperature control accuracy, stable and reliable performance.
◆ Digital display of water temperature Temperature controller, precise, stable, and reliable.
◆ Equipped with automatic control and protection alarm devices, as well as fault signal output.
The water temperature and flow can be adjusted as needed
◆ Easy to operate, capable of long-term continuous work
◆ All stainless steel water tank and water pump The expansion valve automatically throttles.
◆ Adopting efficient shell and tube design to increase heat dissipation area.
◆ Adopting original high-efficiency scroll compressor, safe and energy-saving, low noise
Equipment main structure:
Rack/water tank/shell compressor/shell evaporator/filter/pressure controller
High and low pressure gauge/constant temperature control/water-cooled condenser piping system Electrical control system
Material selection and characteristic description:
The rack is made of Q235A square steel and the outer shell is made of A3 sheet metal, with secondary spraying of colored paint;
The air conditioning unit is a fully enclosed compressor, and the temperature controller is a digital temperature controller;
All other major electrical components are of high quality;
Adopting a water-cooled shell and tube heat exchanger.
The refrigeration system of a chiller unit consists of four basic parts: compressor, condenser, throttle, and evaporator. Connect the four major components in a certain order using copper pipes to form a closed system, which is filled with a certain amount of refrigerant.
The compressor sucks in low-temperature and low-pressure Freon gas from the evaporator, compresses it into high-temperature and high-pressure Freon gas, and then flows through a thermal expansion valve (capillary tube), throttling it into a low-temperature and low-pressure Freon liquid two-phase object. Then, the low-temperature and low-pressure Freon liquid absorbs heat from indoor air in the evaporator, and the cycle of compression condensation throttling evaporation is repeated.
There are 22, 404, 407, and 410 refrigerant models for chillers
410 belongs to high-pressure refrigerant
404 low-temperature refrigerant
407 with environmental protection
Water cooled chillers must be matched with cooling towers
Water cooled chiller factories can customize:
PN4-5PS
PN4-8PS
PN4-10PS
PN4-15PS
PN4-20PS
PN4-25PS
PN4-30PS
PN4-40PS
PN4-50PS